«ЗАРЕМ П» ПРОИЗВОДСТВО АЛЮМИНИЕВОГО ПРОФИЛЯ
История компании «ЗАРЕМ П» началась в 2013 году. 10 лет высококачественной и надежной работы позволили нам выстроить доверительные отношения с нашими клиентами и партнерами по всему миру.
Завод «ЗАРЕМ П» занимается производством алюминиевого профиля архитектурной системы «ALU BOSS» и профилей по чертежам заказчика. Высокое качество готовой продукции на нашем заводе достигается благодаря импортному оборудованию и отточенному технологическому процессу.
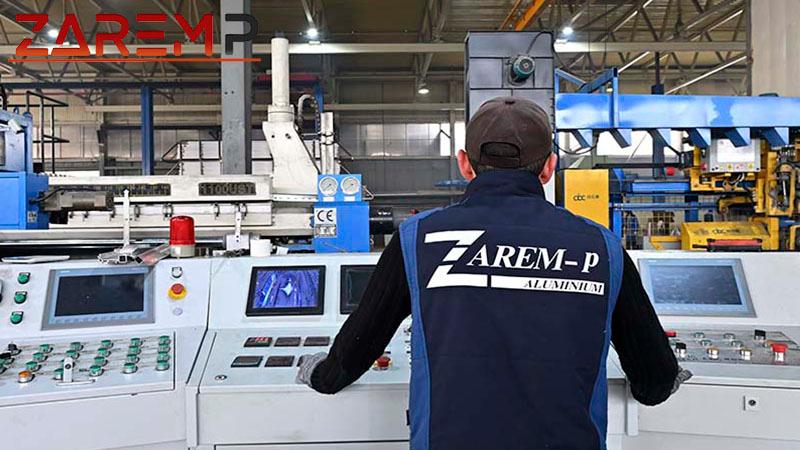
ПРОИЗВОДСТВО АЛЮМИНИЕВОГО ПРОФИЛЯ НА ЗАВОДЕ «ЗАРЕМ П»
Наш завод имеет все возможности для производства продукцию, соответствующую стандартам качества:
Инженерно-конструкторский отдел.Для производства (экструзии) алюминиевого профиля на первом этапе требуется подготовить ряд спецификаций и чертежей, чтобы готовая продукция полностью соответствовала стандартам качества. Команда специалистов завода «Зарем П» имеет многолетний опыт проектирования и производства самых разнообразных видов профиля. Мы готовы прочертить модель изделия любой сложности, при этом Вам может быть достаточно только эскиза. Возможно создание чертежей и запуск из в производство на основе предоставленных Вами образцов профиля.
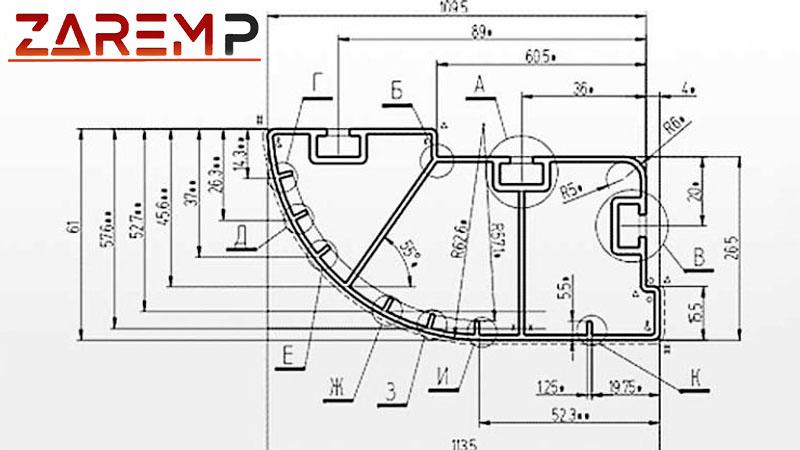
Цех матричного инструмента.Одним из обязательных условий получения качественного профиля является применение высокоточного и надежного прессового инструмента (матриц для экструзии). Матрицы можно изготавливать для неограниченного количества видов профилей. Единственным требованием к профилю является его технологичность с точки зрения прессования. На сегодняшний день ассортимент выпускаемой продукции составляет более 2 тысяч наименований и постоянно увеличивается.
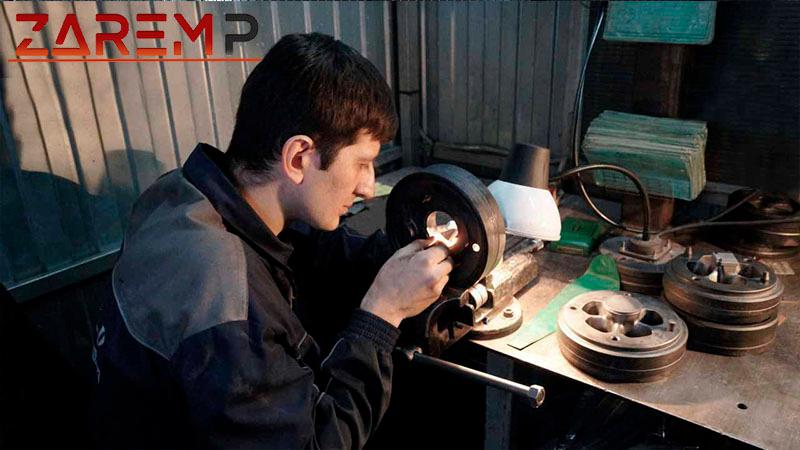
Цех экструзии.Экструзия начинается с заготовки: перед началом прессования отрезок алюминия, из которого формируется профиль, разогревается до температуры 450 градусов цельсия. Затем разогретая заготовка помещается в экструзионный пресс – мощное гидравлическое устройство, в котором полунжер с пресс-шайбой проталкивает размягченный металл сквозь матрицу, что позволяет заготовке принять нужную форму. Изготовление алюминиевого профиля ведется с использованием матричного инструмента, на двух экструзионных прессах производительностью 7,2 тысяч тонн продукции в год.
1-й экструзионный пресс с эллипсообразным выходом и мощностью 1460 тонн, который позволяет произвести профиль по сложным чертежам. Производительность - 3600 тонн в год. Диаметр слитка – 152 мм,
2-й экструзионный пресс с эллипсообразным выходом и мощностью 1100 тонн. Производительность - 3600 тонн в год. Диаметр слитка – 127 мм.
В качестве заготовки используются сплавы 6060, 6063, 6005, АД31, АД1, АД0 и другие.
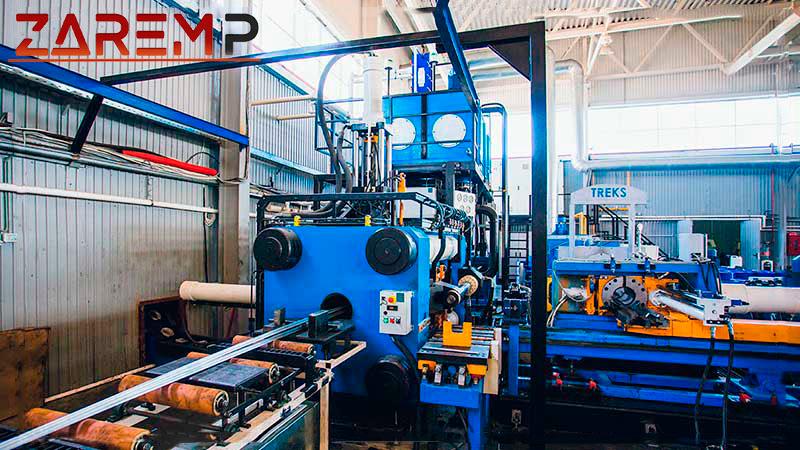
Цех полимерно-порошкового покрытия (система ТРИБО) — 1 горизонтальная линия покраски, мощностью до 450 т. в месяц. Благодаря полимерно-порошковому покрытию профиль защищается от воздействия коррозии, обладает высокой стойкостью к воздействию химических реагентов, солнечных лучей и атмосферных явлений.
Горизонтально расположенный на конвейере профиль при помощи системы напыления равномерным слоем покрывается порошковой краской. Процесс представляет собой нанесение на заземленное изделие электростатически заряженного порошка при помощи пневматического распылителя. Далее профиль направляется в печь, где по заданным параметрам происходит запекание. Мы используем только высококачественные импортные порошковые покрытия полиэфирного типа. Наше оборудование позволяет применять все имеющиеся на рынке порошковые краски любого типа и любого цвета. По желанию клиента можно подобрать любой цвет полимерно-порошкового покрытия по шкале RAL.
Перед окрашиванием применяется многостадийная химическая подготовка алюминиевого профиля, включая такие операции как: обезжиривание, травление и бесцветное хроматирование. После каждой такой операции следует промывка водой. Последняя стадия – промывка деминерализированной водой. Именно такая комплексная подготовка изделий гарантирует отличную адгезию (сцепление) порошкового покрытия с подложкой и хорошую коррозийную стойкость даже при эксплуатации изделий в агрессивной среде.
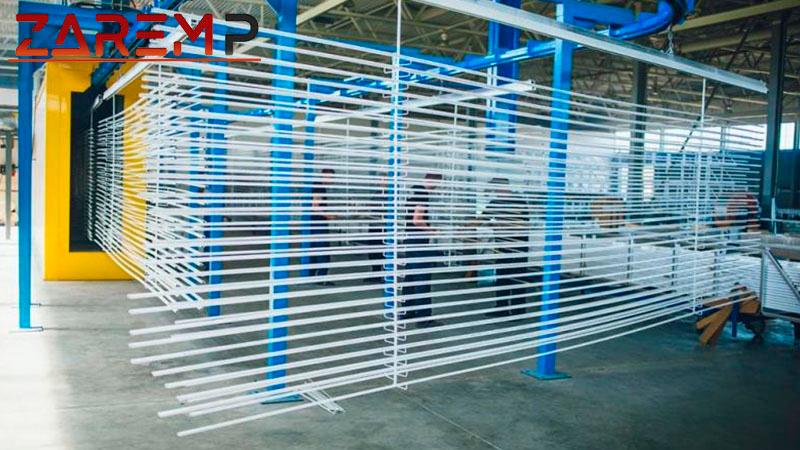
Цех механической обработки профиля:резка профиля по требуемым размерам и нарезка резьбы, сверление технологических отверстий, склеивание соединений, сварка, склепывание, завинчивание, сборка готовых изделий или фурнитуры. На последней стадии происходит упаковка профиля в паллеты с фирменным логотипом ZaremP.
Вся продукция отвечает требованиям ГОСТ и индивидуальным пожеланиям заказчиков. Контроль качества ведется на каждом из этапов производства, а высококвалифицированные специалисты обеспечивают бесперебойную работу и индивидуальный подход к каждому клиенту. Отточенный технологический процесс позволяет работать с нестандартными длинами и сложным окрашиванием в сжатые сроки и гарантировать изготовление заказа по доступной цене.
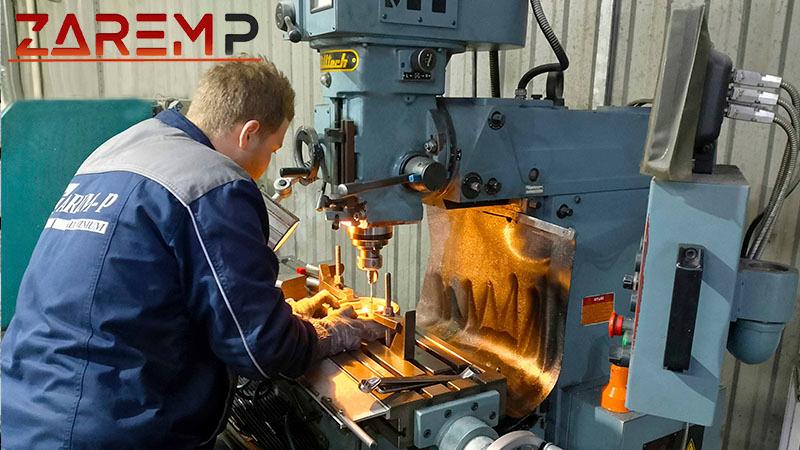
Приоритетной задачей для нашего завода является производство качественного профиля, мы выбираем только надежных поставщиков, занимающих на рынке лидирующие позиции и способных обеспечить поставки сырья, отвечающего самым высоким требованиям.